The Future of Robotics in Logistics and Warehousing
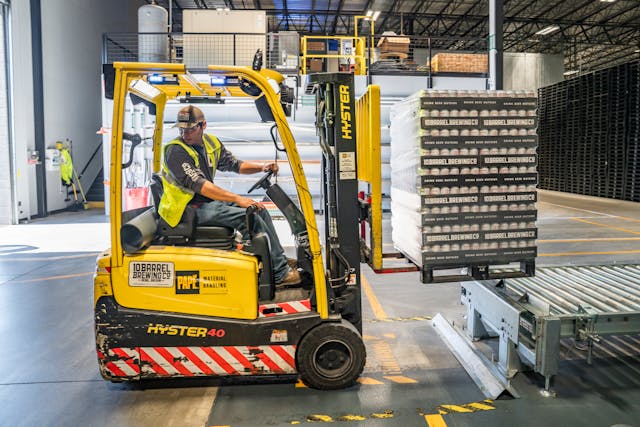
Table of Contents
- Introduction to Robotics in Logistics
- Benefits of Robotics in Warehousing
- Current Technologies
- Challenges and Solutions
- Case Studies
- Future Trends and Predictions
- Critical Considerations for Implementation
Introduction to Robotics in Logistics
Integrating robotics in logistics has revolutionized the industry by enhancing efficiency, reducing costs, and improving accuracy. With advancements in automation in logistics, robots are now handling everything from picking and packing to transportation within warehouses. This shift is fundamentally changing the logistics landscape, making processes more streamlined and reliable.
The use of robotics is changing how commodities are moved, stored, and handled fundamentally rather than being a passing fad. The evolution of these technologies is driven by the need for efficiency, precision, and cost-effectiveness, making robotics an integral part of the modern logistics framework. As companies continue to adopt these technologies, they are setting new standards for what is possible in the realm of logistics.
Robotics brings a wealth of advantages to warehousing, including higher throughput, increased safety, and greater flexibility. For instance, robots can operate 24/7 without fatigue, significantly boosting productivity. Additionally, they can handle dangerous tasks for human workers, thus decreasing the risk of injury and ensuring a safer working environment.
Increased Efficiency and Productivity
Robots are far more efficient than humans at repeated jobs because they can complete them more faster and with greater accuracy. This ability allows businesses to handle more volume without increasing personnel costs. Furthermore, robots can work continuously without breaks, which maximizes output during peak times, contributing to better overall productivity.
Enhanced Safety
Businesses may guarantee a safer working environment for their employees by delegating risky activities to robots. This not only reduces workplace accidents but also improves overall worker satisfaction. For instance, tasks that require lifting heavy objects or working in hazardous conditions can be effectively managed by robots, minimizing risks and injuries.
Current Technologies
Today’s warehouses are equipped with state-of-the-art robotic systems like Automated Guided Vehicles (AGVs) and autonomous mobile robots. These technologies are designed to work alongside human workers, enhancing their capabilities and streamlining warehousing processes. Read more about current trends in robotics for detailed insights.
Additionally, collaborative robots, or cobots, are becoming more prevalent. These robots are designed to work in close quarters with human workers, performing tasks that require a combination of robotic precision and human ingenuity. The seamless integration of these technologies is pivotal in creating more efficient and responsive warehouses.
Challenges and Solutions
While the benefits are substantial, adopting robotics in warehousing comes with its own challenges. These include the necessity for continual maintenance, integration with current systems, and significant initial investment prices. However, companies are finding ways to overcome these issues through strategic planning and leveraging technological advancements.
High Initial Costs
The upfront investment required for robotic systems can be daunting for many businesses. However, it’s important to consider the long-term return on investment. These systems can pay for themselves over time by improving efficiency and reducing labor costs. Moreover, various leasing and financing options are now available, making these technologies more accessible.
Integration and Maintenance
Integrating robots with existing systems can be complex. Effective planning and choosing compatible technologies can ease this process. Though an additional cost, regular maintenance ensures that the systems remain operational and efficient. Periodic training for employees on the latest technologies can also facilitate smoother integration and optimal use of robotic systems.
Case Studies
Several leading companies have successfully integrated robotics into their logistics operations. For example, Amazon’s use of Kiva robots has significantly reduced their operational costs while improving efficiency. Similar success stories from other companies provide valuable insights and validation for the benefits of robotics.
Companies like DHL and Walmart have also made significant strides by integrating logistics robots, allowing them to handle increased demand while maintaining high levels of accuracy and efficiency. These case studies demonstrate the usefulness and advantages of robotics in practical situations.
Future Trends and Predictions
The future of robotics in warehousing promises even more exciting developments. Trends indicate a rise in the use of AI and machine learning to make robots more autonomous and efficient. Moreover, sensor technology and IoT advancements are expected to further revolutionize warehouse operations.
In the near future, we can expect robots to become even smarter, with enhanced decision-making capabilities, enabling them to perform more complex tasks autonomously. These advancements will make warehouses more adaptive and responsive to changing demands, further improving efficiency and productivity.
Critical Considerations for Implementation
Before implementing robotics in warehousing, companies should consider factors such as the specific needs of their operations, budget constraints, and the training required for workers to interact with new technologies. Ensuring a strategic approach can lead to a smoother integration and maximize the benefits of robotic systems.
Operational Needs
Understanding your operations’ specific needs is critical. Not all warehousing tasks may be suitable for automation, and identifying the right tasks can help prioritize investment. Finding the areas where robotics can have the biggest impact requires a detailed review of the workflows and procedures in place.
Budget Constraints
While the initial investment is high, companies should evaluate their budget to see where automation can offer the most significant returns, either by reducing operational costs or increasing throughput. A phased approach to implementation can help manage costs while progressively realizing the benefits of automation.