Manufacturing Clothes: A Complete Guide to the Apparel Production Process
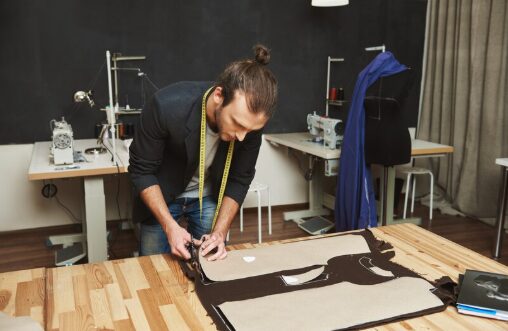
Clothing is an essential part of human life, but have you ever wondered how your favorite t-shirt, jeans, or jacket is made? The process of manufacturing clothes is a fascinating journey that blends creativity, technology, labor, and logistics. From design conception to the final product on store shelves, each garment undergoes a series of complex steps. This article explores everything you need to know about how clothes are manufactured — the processes, materials, challenges, and innovations shaping the apparel industry.
1. Introduction to Clothing Manufacturing
Clothing manufacturing refers to the mass production of garments from raw fabrics and other materials. This process typically takes place in factories and involves a blend of skilled labor and automated machinery. The goal is to transform fabric into finished clothing items like shirts, pants, dresses, coats, and more — efficiently and at scale.
Modern apparel production has grown to accommodate fast fashion, e-commerce, and sustainable initiatives. Manufacturers must balance cost-efficiency, speed, and quality while adapting to consumer demands and global trends.
2. The Design Phase
The journey of manufacturing clothes begins with fashion design. Designers sketch ideas or use software (CAD – Computer-Aided Design) to develop clothing concepts based on market research, seasonal trends, and target audience preferences.
Key components of this stage include:
- Concept creation
- Material research
- Color palette selection
- Sketching and digital illustrations
- Tech pack development (blueprints for production)
Tech packs include measurements, stitching details, trims, and labeling guidelines, serving as a communication tool between designers and manufacturers.
3. Fabric Selection and Sourcing
Once the designs are finalized, the next step is to source fabrics and trims. The type of fabric used will significantly impact the garment’s look, comfort, and durability.
Popular fabric types:
- Natural fibers: Cotton, wool, silk, linen
- Synthetic fibers: Polyester, nylon, spandex
- Blended fabrics: Cotton-polyester blends, viscose, rayon
Manufacturers often partner with textile mills or fabric suppliers locally or overseas to procure materials in bulk.
Fabric sourcing considerations:
- Cost per meter
- Minimum order quantity (MOQ)
- Dyeing and printing compatibility
- Lead times and shipping
4. Pattern Making and Grading
Pattern making is the art of converting design sketches into templates used to cut the fabric. These templates are the building blocks of a garment.
- Manual Pattern Making: Drafted by hand on paper or cardboard.
- Digital Pattern Making: Created using specialized software for precision and scalability.
Grading
Once the base pattern is ready, it is graded to produce different sizes (e.g., XS to XXL) while maintaining the correct proportions.
5. Fabric Cutting Process
Fabric is laid out on long cutting tables in multiple layers to increase efficiency. Patterns are placed strategically to minimize fabric wastage.
Cutting Methods:
- Manual Cutting: Scissors or handheld cutting machines.
- Die Cutting: Uses pre-shaped metal blades.
- Laser Cutting: High-precision method using laser beams for clean edges.
Cutting is a crucial stage because errors here can cause significant material loss and affect garment symmetry.
6. Garment Sewing and Assembly
The cut fabric pieces are now sent to the sewing department, where skilled workers assemble them into full garments.
Assembly involves:
- Joining panels (e.g., attaching sleeves to bodies)
- Adding fasteners (zippers, buttons, hooks)
- Stitching hems, cuffs, collars
- Embellishments like embroidery or prints
This phase often employs assembly-line production, where each worker is responsible for a specific task to speed up the process.
7. Quality Control in Clothing Manufacturing
Before garments are packed and shipped, they go through rigorous quality control (QC).
QC checkpoints:
- Stitch accuracy
- Seam strength
- Size compliance
- Color consistency
- Defect identification (holes, stains, irregularities)
Defective garments are either repaired, sold at discount, or recycled.
8. Finishing and Packaging
Once QC is cleared, garments undergo finishing:
- Ironing or steaming to remove wrinkles
- Trimming loose threads
- Adding brand tags, size labels, and price tags
Finally, clothes are folded, packaged, and packed into boxes ready for shipment to retailers or distribution centers.
9. Sustainability in Clothing Production
The fashion industry is under growing pressure to reduce its environmental footprint. Sustainable clothing manufacturing focuses on:
- Using eco-friendly fabrics (e.g., organic cotton, bamboo, recycled polyester)
- Waterless dyeing and low-impact processes
- Reducing fabric waste through digital patterning
- Ethical labor practices and fair wages
- Recycling and upcycling unused garments
Many brands are also exploring circular fashion, where clothing is designed for reuse, repair, or recycling at the end of its life.
10. Common Challenges in Apparel Manufacturing
Despite technological advances, clothing manufacturing faces several ongoing challenges:
Labor Issues
- Poor working conditions in developing countries
- Sweatshops and child labor
- Skilled labor shortages
Supply Chain Disruptions
- Raw material delays
- Political instability or trade tariffs
- COVID-19-related lockdowns
Quality Consistency
Maintaining the same quality across batches and sizes is a significant hurdle, especially when outsourcing.
Environmental Impact
Water pollution, excessive energy use, and textile waste are ongoing concerns.
11. The Future of Clothing Manufacturing
The apparel industry is evolving rapidly due to technology and consumer expectations.
Trends to watch:
- Automation and robotics in sewing
- 3D printing of garments
- AI-powered demand forecasting
- On-demand manufacturing (producing only when ordered)
- Smart fabrics with tech integration (wearable tech)
- Local micro-factories for faster shipping and lower emissions
Brands that embrace digital transformation, eco-conscious materials, and efficient production models will lead the next wave of fashion manufacturing.
12. Conclusion
Manufacturing clothes is a complex but rewarding process that involves design thinking, technical precision, and global collaboration. From raw fabric to retail-ready garments, every step demands attention to detail, quality control, and adaptability to market needs. As the industry continues to transform with technology and sustainability goals, understanding the ins and outs of apparel production becomes even more important — whether you’re a fashion designer, business owner, or curious consumer.
13. FAQs
Q1: How long does it take to manufacture clothes?
It depends on the garment and the scale of production. A simple t-shirt might take a few hours, while more complex items like jackets can take days. For bulk orders, lead times can range from 2 to 12 weeks.
Q2: What’s the minimum order quantity (MOQ) in clothing manufacturing?
MOQs vary by factory and product type. For small brands, MOQs can be as low as 50 pieces per style. Larger factories may require 500–1000 units per design.
Q3: Can I start a clothing line without my own factory?
Yes. Many entrepreneurs work with private label manufacturers or OEM/ODM clothing factories to produce custom garments without owning production facilities.
Q4: What is the most sustainable fabric for clothing manufacturing?
Organic cotton, hemp, Tencel, and recycled polyester are considered some of the most sustainable options, depending on how they are processed.
Q5: What are the best countries for clothing manufacturing?
China, Bangladesh, India, Vietnam, Turkey, and Indonesia are among the top clothing manufacturers globally due to their infrastructure, skilled labor, and competitive costs.